Manufacturing supply chain redesign and reconfiguration for resilience
Sep 07, 2023 • 9 min read
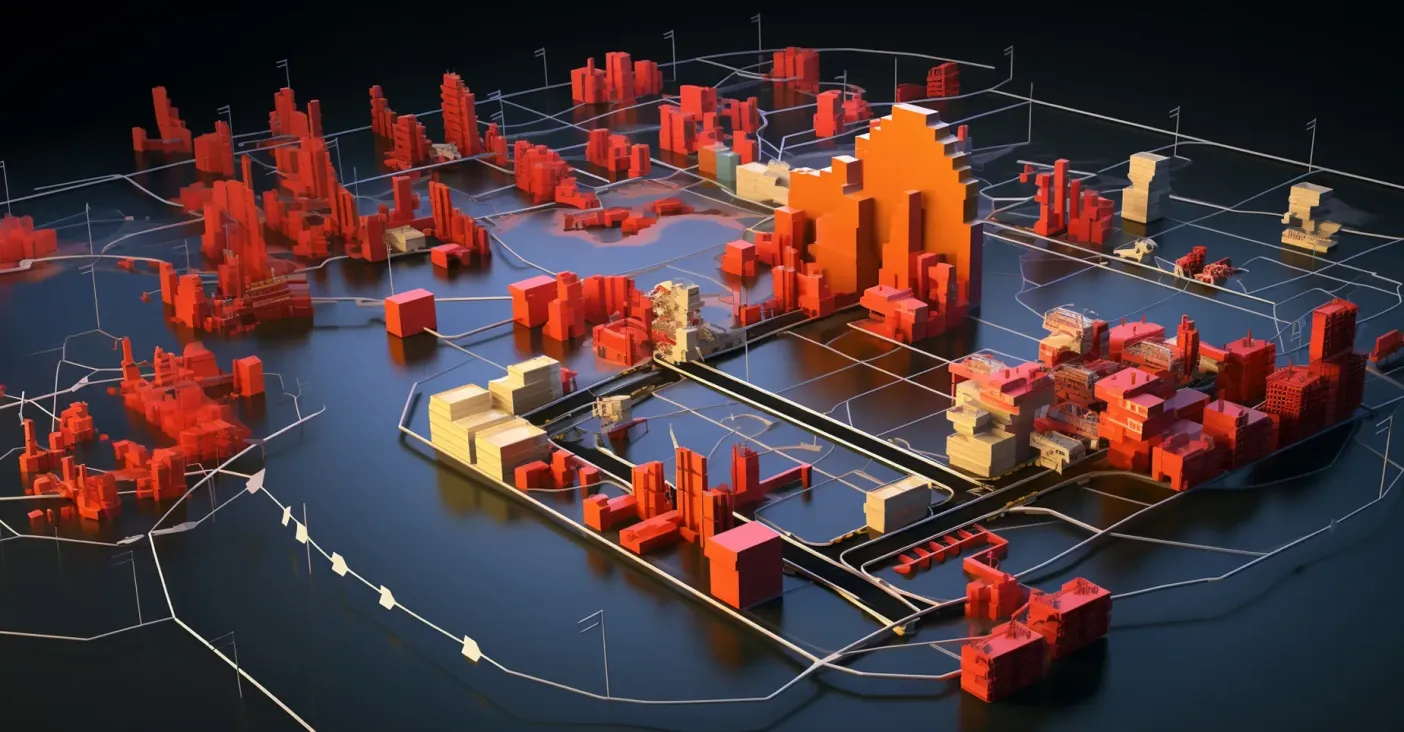
- Striking the balance: Supply chain redesign for resilience amidst uncertainty and competition
- Benefits of supply chain reconfiguration
- Focus area: Reducing supplier concentration
- Focus area: Transforming the manufacturing footprint
- Focus area: Enabling elastic logistics
- Modularity in supply chain redesign: Composability over monolith
- Key thoughts on steps to reconfigure supply chain
- Conclusion
Can a mere joke trigger a catastrophic product supply shortage? Can mischievous squirrels wreak havoc on large-scale business operations? And what’s the connection between beer, road closures, and transportation delays? These may seem like bizarre scenarios (see the postscript at the end of this blog for real-life examples), but the consequences are far from amusing. Supply chain disruptions, regardless of their peculiar origins, can result in significant profit losses and reputational damage, demanding substantial time and effort to recover from. In this article, we delve into the crucial topic of redesigning and reconfiguring manufacturing supply chains for resilience. Our aim is to empower manufacturers to maintain uninterrupted operations during turbulent times and to enhance their competitive standing in a normal business environment.
Within the context of our modular framework for supply chain resilience, we will explore three key aspects in this blog:
- Balancing resilience and efficiency: One of the primary challenges in supply chain management is finding the delicate equilibrium between resilience and operational efficiency. While striving for maximum efficiency can lead to cost savings and streamlined processes, it may also render the supply chain vulnerable to unforeseen disruptions. We will examine why striking this balance is imperative for long-term sustainability and success.
- Areas of focus for safeguarding the bottom line: To ensure business continuity and profitability, manufacturers need to identify and prioritize areas where they can fortify their supply chains. We will discuss key areas of focus, such as supplier diversification, demand forecasting, and risk mitigation strategies, all aimed at safeguarding the bottom line.
- Harnessing technology for augmented operations: In an era of rapid technological advancements, the integration of technology into supply chain operations is pivotal. We will explore how cutting-edge technologies like artificial intelligence, IoT, and blockchain can augment human decision-making and streamline processes. Additionally, we’ll delve into real-world examples showcasing the transformative power of technology in supply chain management.
Striking the balance: Supply chain redesign for resilience amidst uncertainty and competition
In a landscape where material supply and demand are shrouded in uncertainty, the prudent approach often shifts from the lean “Just-In-Time” model to a more cautious “Just-In-Case” strategy. This entails stockpiling extra inventory for critical items and adopting measures like maintaining low-capacity utilization and collaborating with multiple suppliers. A pivotal element in this strategy is supplier diversification, which serves as a safeguard against disruptions stemming from geopolitical risks. While these precise actions are widely acknowledged as crucial for building supply chain resilience, companies frequently find themselves hesitating to take robust measures. This hesitancy is driven by the complex interplay of factors, including the quest for competitive advantages in the midst of economic downturns.
Supply chain managers are perpetually confronted with a challenging dilemma: striking the optimal balance between maintaining safety stocks and staying competitive. This entails making strategic decisions regarding the allocation of financial and operational resources. The goal is to create a buffer that enhances resilience without unduly inflating supply chain costs during periods of regular performance.
Key considerations:
- Embracing Just-In-Case amidst uncertainty: In an environment characterized by volatile supply and demand dynamics, adopting a Just-In-Case approach is often the safest course of action. This involves holding extra inventory for critical items, which acts as a safety net against disruptions. Additionally, maintaining low-capacity utilization and cultivating relationships with multiple suppliers contribute to bolstering resilience. Supplier diversification, specifically, mitigates the risk associated with the potential disruption of critical supply links due to geopolitical factors.
- The competitive imperative: Despite the imperative of enhancing resilience, companies face the ever-pressing need to identify competitive opportunities, even during economic recessions. This dual challenge underscores the complexity of supply chain management decisions. Supply chain managers must navigate the delicate balance between safeguarding against shocks and positioning the company to thrive amidst competition.
As Forbes has highlighted, the critical challenge we face is maintaining a delicate equilibrium between efficiency and resilience. In light of this, it is imperative that we invest in enhancing resilience while simultaneously driving business profitability.
Furthermore, disruptions in today’s business landscape are growing both in frequency and impact. Following the profound disruption caused by the COVID-19 pandemic, the ongoing conflict in Ukraine remains a significant risk factor. In addition to geopolitical concerns, there are local disruptions that can significantly affect logistics management and lead times, such as the Hong Kong protests and the more recent bankruptcy announcement from transportation provider, Yellow.
To fortify supply chains and improve their resilience, it is crucial to adopt a strategy that prioritizes transparency, real-time visibility, and automated alerting systems. These measures not only assist in informed decision-making but also draw attention to heightened risks of potential disruptions, allowing for proactive responses.
Benefits of supply chain reconfiguration
When discussing the redesign of a supply chain, the best course of action is to base decisions on a value-risk trade-off. This segment of the supply chain resilience framework is centered on areas and actions that not only enhance resilience but also contribute to operational efficiency and the discovery of new opportunities and partnerships. Let’s delve into the focal points outlined in Table 1:
Focus areas | Resilience benefits | Business profitability |
Supplier diversification | ||
Manufacturing footprint transformation | ||
Elastic logistics |
Table 1: Benefits of supply chain reconfiguration
Let’s delve into each of the focus areas in more detail and assess the necessary capabilities that manufacturers must cultivate to foster innovation while maintaining a delicate balance between resilience and efficiency.
Focus area: Reducing supplier concentration
Diversifying procurement and sourcing strategies by engaging with multiple suppliers enhances a manufacturer’s adaptability in the face of dynamic business conditions and unforeseen disruptions.
Key considerations:
- Incorporating geopolitical risk awareness: Factoring in geopolitical risks and reconfiguring the supply chain focus from purely cost optimization to a more adaptable global model.
- Embracing diverse sourcing approaches: Leveraging nearshoring, onshoring, and ally shoring as core strategies to enhance supplier diversity and reduce vulnerability.
- Continuous supplier risk assessment: Implementing a robust supplier risk monitoring and assessment system to identify potential vulnerabilities and proactively address them.
Technology requirements:
- Data resilience and analytics: Establishing a robust data infrastructure across the supply chain and employing purpose-based data analytics to gain insights into supplier performance and risk.
- Data standardization: Standardizing data gathering processes from supplier networks to facilitate the seamless onboarding of new suppliers and ensure data consistency.
- Cybersecurity and sustainability standards: Maintaining a strong stance on cybersecurity and sustainability (ESG) standards and fostering shared policies within the supply chain network to enhance security and sustainability practices.
Focus area: Transforming the manufacturing footprint
Strategically altering manufacturing processes or relocating facilities demands meticulous planning, but it yields substantial benefits in terms of bolstering stability and capitalizing on the advantages that innovation and process enhancement can bring.
Key considerations:
- Balancing AI, PI, and HI: Striking the right equilibrium between Artificial Intelligence (AI), Process Intelligence (PI), and Human Intelligence (HI) to optimize manufacturing operations.
- Embracing advanced technologies: Incorporating automation, IoT (Internet of Things), and advanced computer vision techniques for quality control to enhance manufacturing efficiency.
- Evaluating in-house vs. contract manufacturing: Deliberating the trade-off between maintaining manufacturing in-house and outsourcing to contract manufacturers based on specific operational and strategic considerations.
Technology requirements:
- Investment in demand planning capabilities: Allocating resources towards technology investments in demand planning capabilities, including real-time analytics. This empowers organizations to maintain operational stability by leveraging AI, particularly in optimizing inventory allocation and streamlining order fulfillment, including allocation to promise (ATP). Additionally, automating order management processes can drive operational efficiency.
- Establishment of an integrated control tower: Implementing a comprehensive control tower spanning industrial, logistics, and financial systems. This integrated system, comprised of data stacks, planning stacks, and reporting stacks, provides end-to-end visibility across the supply chain. Its exceptional exception-based management capability aids in proactively addressing issues.
- Real-time data capture for ESG metrics: Capturing real-time operational data throughout the supply chain to facilitate measurement and reporting of Environmental, Social, and Governance (ESG) metrics. This transparency enables organizations to monitor and enhance their sustainability initiatives effectively.
Focus area: Enabling elastic logistics
The ability to adapt logistics and infrastructure in response to demand fluctuations is a pivotal capability that enhances both resilience and the achievement of business objectives. Leveraging real-time data and insights for route planning and optimization allows for the efficient allocation of resources, thereby promoting goals like on-time and in-full delivery and expediting order fulfillment.
Key considerations:
- Digitization of logistics processes: Embracing the digital transformation of logistics processes to enhance visibility, efficiency, and adaptability in a rapidly changing environment.
- Comprehensive optimization: Implementing multimode transport, optimizing carrier space and container usage, and automating quality control to ensure flexibility and efficiency.
- Focus on last-mile delivery and reverse logistics: Placing increased emphasis on last-mile delivery and the intricacies of reverse logistics, particularly in the context of e-commerce serving both B2C and B2B businesses.
Technology requirements:
- Integration of Autonomous Mobile Robots (AMRs) and Automated Guided Vehicles (AGVs): Incorporating autonomous mobile robots and AGVs for tasks such as picking, assembling, carrying, packing, or inspecting parts and finished products. These technologies streamline operations and enhance efficiency.
- Investment in logistics platforms: Investing in or partnering with logistics platforms that extend beyond automation to encompass digitization of key services. This includes enhancing the customer experience, enabling functions such as rating, quoting, booking, and shipment tracking, as well as managing returns seamlessly.
- Harnessing AI/ML for enhanced management: Leveraging the power of Artificial Intelligence (AI) and Machine Learning (ML) for optimizing spare parts inventory management and planning. Additionally, these technologies can be applied to lucrative aftermarket service operations, enhancing overall efficiency and profitability.
Modularity in supply chain redesign: Composability over monolith
Just as Rome wasn’t built in a day, comprehensively reconfiguring the supply chain design is not a task that can be accomplished with a single effort. This underscores the importance of considering the state of IT/OT (Information Technology/Operational Technology) infrastructure. Monolithic platforms function in a similar manner to a supply chain reliant on a few suppliers. While a unified solution offers certain advantages, it poses a significant threat to business resilience. Likewise, monolithic solutions come with their benefits, but they lack future-proofing and become increasingly challenging to manage and adapt over time.
Challenges associated with monolithic solutions include:
- System-wide downtimes: Downtimes that impact the entire system, causing disruptions in operations.
- Slow scalability, upgrades, and maintenance: Delays in scaling up, implementing upgrades, and conducting maintenance tasks, resulting in inefficiencies.
- Innovation bottlenecks: Lengthy coordination and implementation times for innovation initiatives, as they impact the entire ecosystem.
- Limited flexibility and integration: Reduced flexibility and difficulty in integrating with external applications or services, leading to inefficiencies and restricted adaptability.
- Talent sourcing and onboarding challenges: Difficulties in finding and onboarding talent proficient in managing monolithic solutions.
To effectively manage supply chains, manufacturers must have granular control over the prioritization and precision of updates in various functional areas. For instance, they should be able to innovate core supply chain ERP capabilities, and complement them with planning systems that address specific process capabilities, all while maintaining data separation to avoid lock-in.
A significant and vital component of the resilient network roadmap involves transitioning away from monolithic supply chain software solutions toward more flexible, resilient, and composable supply networks. Modern cloud applications, such as those based on microservices or composable architecture, enable the weaving together of solutions tailored to specific business and supply chain needs, rather than relying on the notion of a “one-stop shop for all your needs” solution.
Alternatively, when considering Commercial Off-The-Shelf (COTS) solutions, it is crucial to evaluate their offerings both in manufacturing use cases and from a technological perspective.
Key thoughts on steps to reconfigure supply chain
In summary, the steps to reconfigure the supply chain involve addressing various components within the modular framework for building resilience within the manufacturing supply chain. These components are mutually exclusive and collectively exhaustive (MECE), as depicted in Figure 3, with each part augmenting and empowering the others:
- Robust data
- Cyber security
- Actionable and measurable sustainability
- Control tower to power business decisions
- Proactive risk monitoring and management
Conclusion
In summary, the approach to building resilience in response to evolving challenges should include factors such as:
- Balancing efficiency and resilience: Striking the right equilibrium between operational efficiency and resiliency.
- Navigating global vs. local supply chain strategies: Strategically reevaluating global and local supply chain strategies to adapt to changing dynamics.
- Managing internal and external risks: Developing strategies for the effective management, mitigation, and recovery from both internal and external risks that can disrupt supply chains.
Furthermore, technological advancements are introducing transformative changes in the way we work, which in itself represents a disruption but also presents new opportunities.
Here are key takeaways for using the framework to reconfigure supply chains for enhanced resilience:
- Prepare and plan for recovery: Assess the supply chain to identify its weakest links. Strengthening the weakest link first is a sensible approach, as it directly enhances overall resilience. Subsequently, focus on fortifying the second-weakest link.
- Consistent and systematic modular actions: Adopt a consistent and systematic approach to implementing modular actions. This approach often yields superior results compared to the “big bang approach,” where extensive changes are made all at once.
If you have questions or would like to delve into these concepts in more detail, please feel free to reach out for further discussion.
P.S. Hilarious incidents still lead to serious losses
As mentioned in the beginning of this blog, some disruptions, differing in scale, can start from quite peculiar events. Let’s take a look at some of them:
- Toilet paper shortage, caused by misunderstanding, panic buying, and a joke by Johnnie Carson. Quite interestingly, such drastic demand spikes occur time and time again (let’s remember COVID, for example), and prolonged shortages lead to government-level actions.
- Squirrels cause power outages all over the globe. There was even an initiative that mapped animal attacks on a world map, and the American Public Power Association wrote a public letter to squirrels. Beer tanker crashing, though local, disrupts logistics and causes losses. For example, see US (2022, 2023) or Germany (2019).
Tags
You might also like
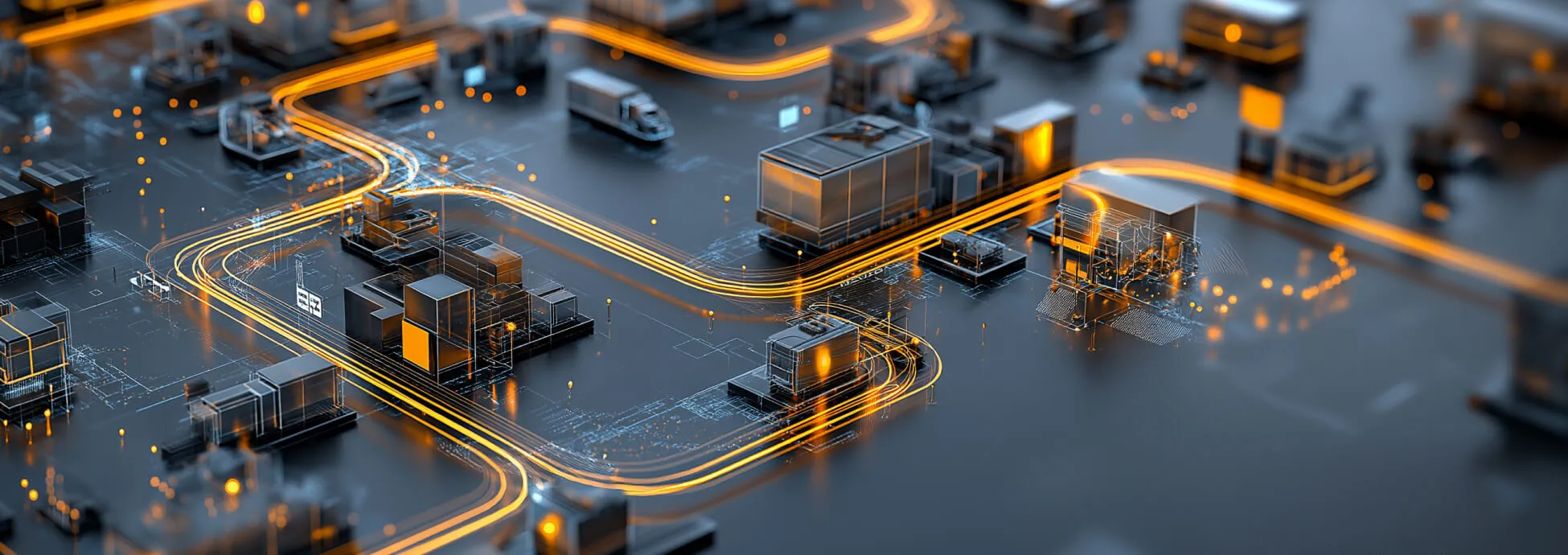
Tariffs, shifting trade policies, and geopolitical instability have slowed new car sales and made consumers more cautious about big-ticket purchases, but the automotive aftermarket continues to surge. With over 2 billion vehicles on the road and rising demand for preventive maintenance, the industr...
The buzzword “composable commerce” has dominated digital strategy conversations since Gartner popularized the term in 2020. But behind the marketing hype lies a longstanding, proven practice of integrating specialized, best-of-breed technology components into a flexible and scalable ecosystem....
In today's fast-paced and data-driven world, accurately predicting demand is more critical than ever for businesses aiming to stay competitive. Traditional forecasting methods often provide a single-point estimate, which can be useful but falls short in accounting for the inherent uncertainties and...
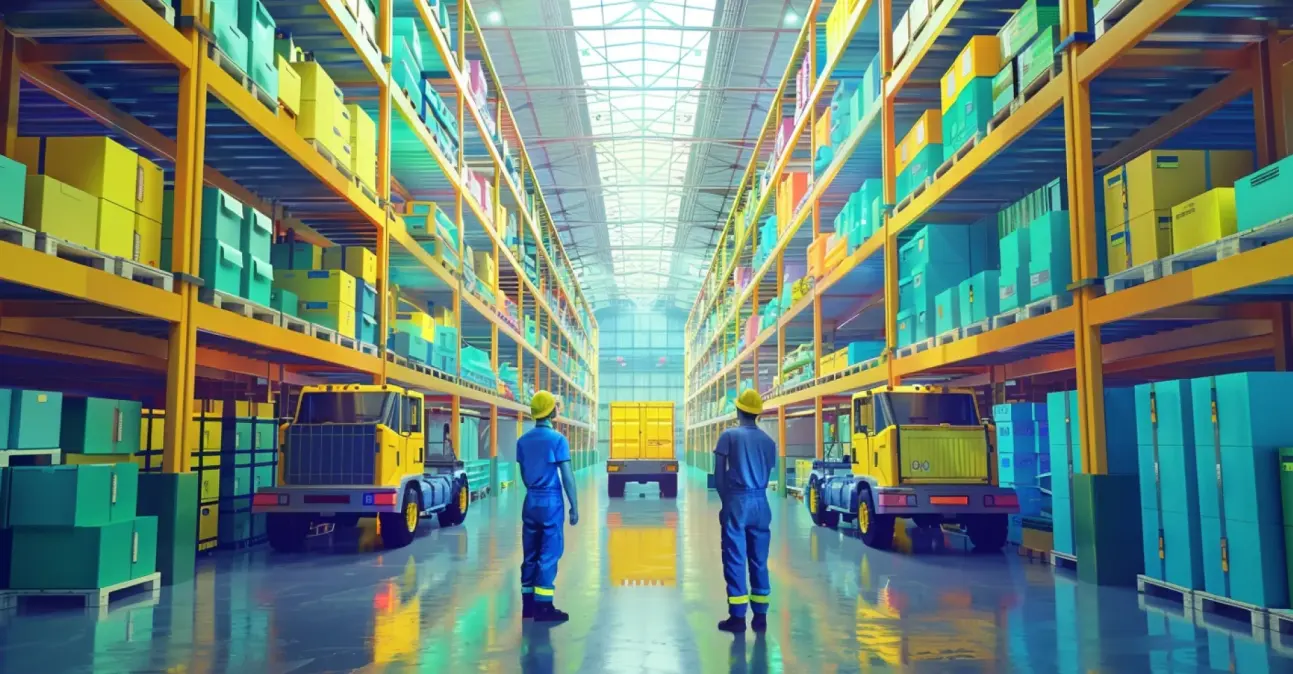
During the pandemic, many manufacturers encountered sudden demand shifts and supply chain disruptions, affecting everything from raw materials to finished products. And until recently, the Baltimore port incident triggered widespread delays in cargo handling, affecting industries from automotive to...
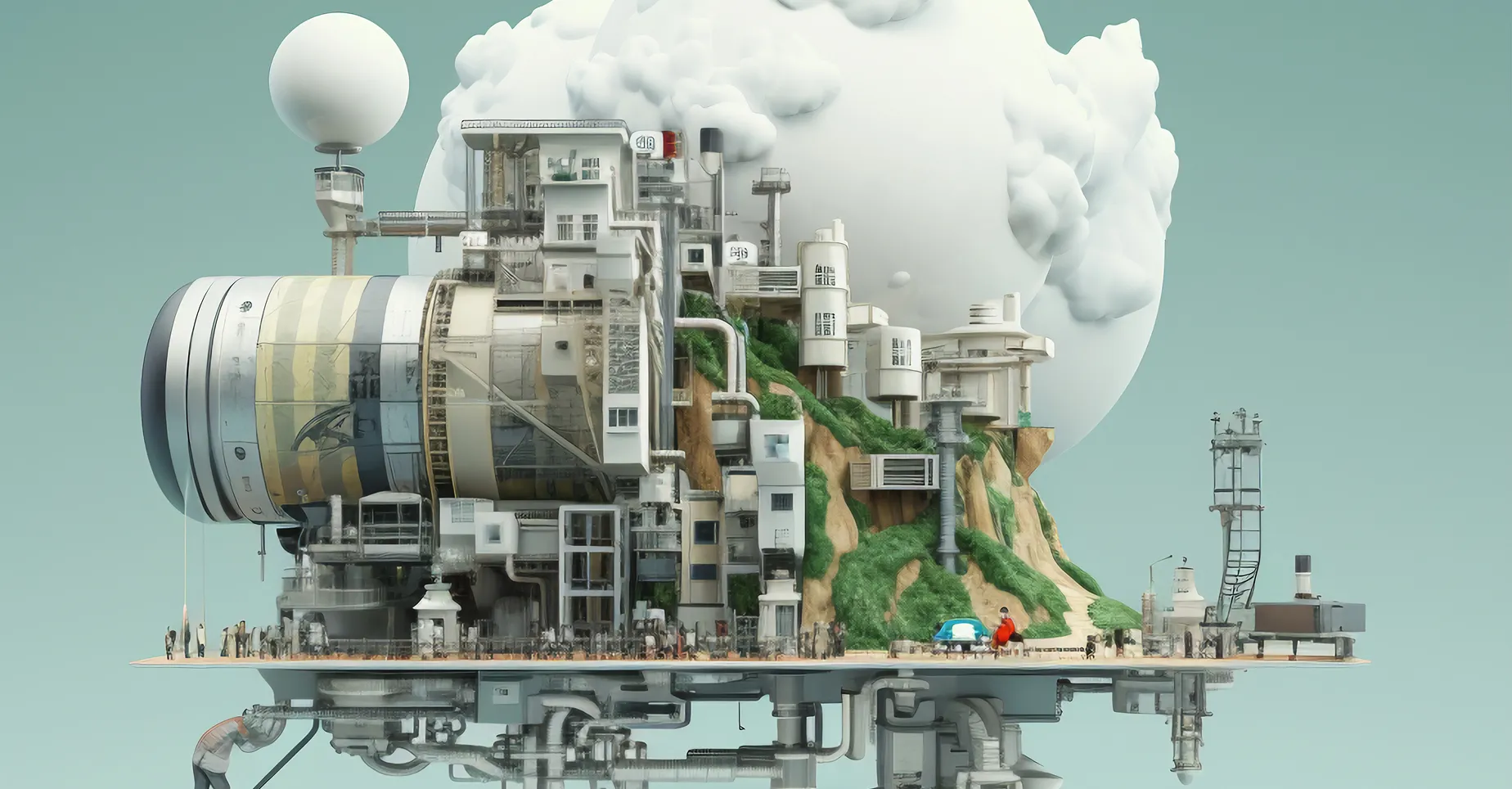
Contract manufacturing involves outsourcing production to third-party manufacturers, which allows companies to focus on core competencies such as design, branding, and distribution. The global contract manufacturing market was valued at USD 246.51 billion in 2022 and is expected to reach USD...
Demand forecasting is a crucial aspect of retail supply chain management that involves predicting future customer demand to make informed decisions about inventory levels, production, and resource allocation. It is a statistical analysis that considers numerous variables to optimize the predict...
In the ever-evolving landscape of transportation, modern Electric Vehicles (EVs) and Hybrid Electric Vehicles (HEVs) have transcended traditional notions of mobility. Beyond mere modes of transportation, these vehicles have emerged as platforms for innovation, where cutting-edge technologies redefi...